NOVOS CONCEITOS QUE TRAZEM MELHORIA NA QUALIDADE E NA PRODUTIVIDADE
Sistemas automáticos de inspeção da impressão com câmeras são hoje empregados com crescente frequência na garantia de qualidade, na efetiva produtividade e redução do descarte. Historicamente eles eram utilizados principalmente para a inspeção final dos produtos em revisoras especiais e em máquinas de acabamento. Se o sistema detectasse um defeito, a revisora parava e este era observado pelo operador, para corrigi-lo. É claro que esse modelo envolve uma série de desvantagens, entre eles os custos de investimento disponíveis, a necessidade de parar e posicionar todos os defeitos.
Maior custo-eficácia é alcançado se o sistema de inspeção da impressão for instalado na impressora. Assim, o impressor pode alcançar objetivos como: qualidade definida e consistente; aumento da produtividade e, como consequência, a redução de custos; vantagens sobre a concorrência.
Este artigo mostra um estudo realizado pela X-label já há algum tempo, mas que continua extremamente válido nos dias atuais. A X-label é uma tradicional convertedora alemã de banda estreita que atua desde 1991 e possui cinco fábricas na União Europeia.
Estamos falando de uma solução de workflow, em que uma ligação em rede de todos os sistemas de inspeção na impressora e na revisora, conectado a um departamento de qualidade central e a uma rede de computadores, traz novos conceitos, baseados em um sistema de inspeção 100 por cento da impressão que aponta melhoria na qualidade e na produtividade.
O trabalho realizado pela convertedora alemã mostra que a aquisição de dados central não só deve cobrir os dados de produção, mas também incluir imagens de inspeção de impressão como uma medida de garantia de qualidade. Esta configuração produziu um elevado grau de transparência e aumentou a produtividade de cada máquina individual. A qualidade fornecida não fica ao critério do operador, mas é claramente definida pelo controle de qualidade. Durante esse processo, o sistema de inspeção 100 por cento da impressão foi integrado diretamente ao de aquisição de dados existente da produção da X-label.
1 – A escolha de um sistema de inspeção em rede
Após uma série de testes com vários sistemas de inspeção da impressão, a X-label chegou à conclusão de que a única opção era uma abordagem holística com estações padronizadas para os quais não era necessário definir previamente atribuição de trabalho. Cada impressora foi equipada com um sistema de inspeção da impressão e teve uma interface com o seu departamento de TI para aquisição dos dados de produção. Os objetivos mencionados anteriormente foram então expandidos com os seguintes parâmetros:
1) Deve ser possível planejar a produção de forma independente, exceção apenas das larguras operacionais e etapas dedicadas de trabalho e técnicas de impressão.
2) Os operadores devem trabalhar para atender às necessidades comuns de controle de qualidade. Por sua vez, decide em uma etapa de trabalho dedicada, se a produção é aceitável ou descartada.
3) Defeitos individuais são identificados e diferenciados dos defeitos aceitáveis ??pelo pessoal de controle de qualidade, por meio do relatório da bobina.
4) Áreas de descarte, no início, fim ou durante a impressão, são definidas com precisão no relatório da bobina – marcações na bobina não são mais necessárias.
5) A revisora usa o relatório da bobina editado pelo controle de qualidade para controlar automaticamente a revisora.
6) Cada trabalho é aberto em cada estação, usando um scanner de código de barras, resultando em completa integração com o sistema ERP da empresa.
Um sistema de inspeção da impressão é instalado em todas as impressoras na fábrica. O arquivo PDF é acessado diretamente pela pré-impressão. Os resultados, os chamados relatórios da bobina, são enviados por meio da rede de dados para um computador central, de onde podem ser administrados pela equipe do controle de qualidade e editado para o processo restante. Os relatórios da bobina editados são abertos na revisora para preparar e finalizar as bobinas, conforme necessário.
2 – O processo de um sistema de inspeção em rede
Uma vez que a ligação em rede das diferentes estações foi descrita, a questão é, então, a forma de controlar o processo. Aplica-se o princípio básico em que o fluxo de material resulta em outro de dados: primeiramente uma bobina é impressa e, simultaneamente, inspecionada. Após a finalização, uma etiqueta codificada com o nome da bobina ou do trabalho é aplicada. A Figura 1 mostra o exemplo de uma etiqueta.
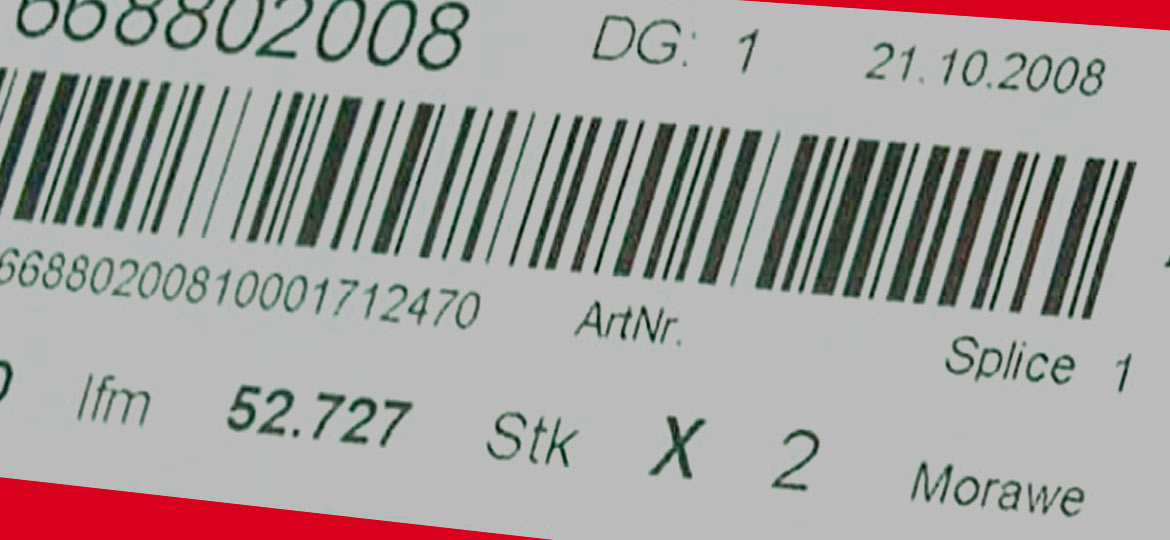
O operador da impressora agora lê o código com a ajuda de um scanner de código de barras. Dessa forma, o nome e os dados específicos da bobina para o trabalho relacionado são alocados para o relatório da bobina. A transferência de dados para o servidor central é iniciada automaticamente; a partir de então o relatório da bobina para qualquer outra pode ser aberto utilizando um scanner de código de barras. O resultado dessa “leitura” é mostrado. Se a verificação não for bem sucedida, as informações também podem ser inseridas ou corrigidas manualmente.
Logo que os dados são guardados no computador central, cada ação subsequente é iniciada pela presença de uma bobina física na estação relacionada. Assim, quando a bobina chega ao controle de qualidade, que é identificada pela digitalização do código de barras, o seu relatório é carregado automaticamente e é então possível começar a editá-lo. Depois disso, concluindo assim o processo, a bobina segue para o acabamento, onde novamente é identificada por meio do código de barras e, em seguida, finalizada com base na informação do controle de qualidade.
3 – O processo de inspeção em rede integrado à pré-impressão
Um sistema automático de inspeção da impressão se baseia em uma comparação da imagem em movimento com outra de referência. O melhor método seria, evidentemente, usar a arte PDF original diretamente como uma referência. No entanto, essa obra não corresponde exatamente à imagem impressa, mas difere em elementos essenciais, como a precisão da cor, representação diferente em filmes, rotulagem, entre outros, e muitas vezes na posição dos elementos individuais.
Para validar a inspeção com a ajuda da arte PDF, é necessário adaptar a mesma para a impressão real. Primeiro, é da maior importância que a câmera de inspeção possa detectar “todos” os recursos de impressão. Esse requisito diz respeito, por exemplo, a filmes metalizados altamente reflexivos que podem ser reproduzidos em sua cor natural, utilizando uma nova tecnologia de iluminação. A Figura 2 mostra a imagem da câmera para uma etiqueta com efeitos diferentes e, à direita, a arte em PDF.
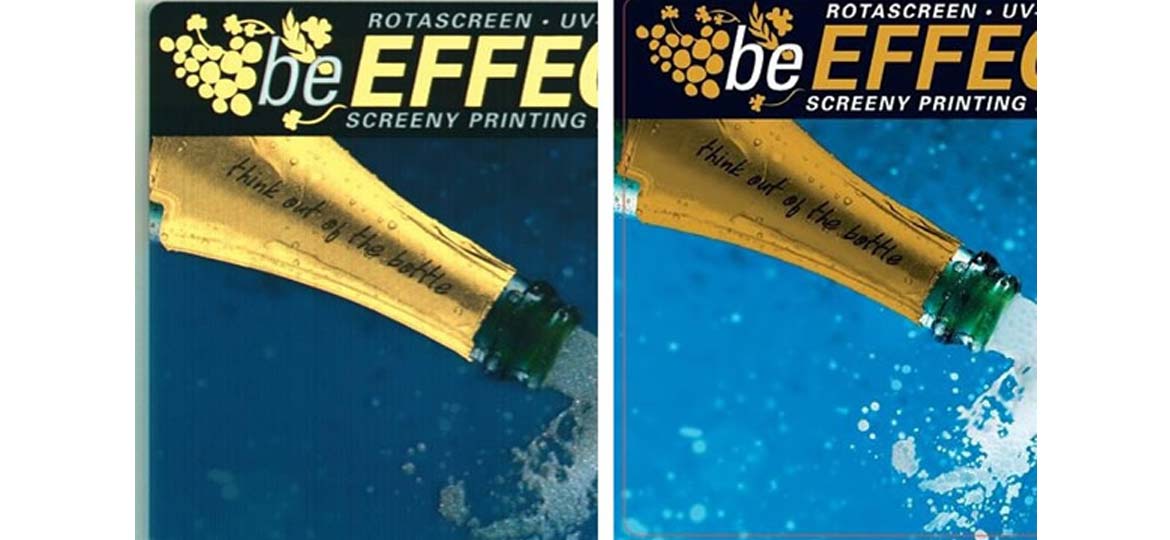
É possível observar a diferença significativa entre as duas imagens que, primeiramente, deve ser compensada pelo sistema de inspeção módulo “Pré-impressão”, substituindo as cores das camadas relevantes, antes da consistência da impressão poder ser verificada com base no PDF. A arte em PDF já separada em camadas do existente workflow da X-label é usada aqui como base.
4 – O que ocorre nas estações individuais do processo em rede
A inspeção é definida pela primeira vez na impressora durante a fase de setup. Para esse efeito, uma imagem de referência é tomada a partir da banda em movimento. Antes do início da impressão, todos os parâmetros importantes e zonas de inspeção foram definidos. Durante a produção o operador pode obter informações sobre a qualidade desde o início até o ponto atual usando o relatório da bobina atual. Como resultado, por exemplo, no caso de um defeito repetitivo no monitor, o operador pode decidir parar a impressora para corrigi-lo. A integração de um sistema de inspeção da impressão em máquina na X-label pode ser visto na Figura 3.
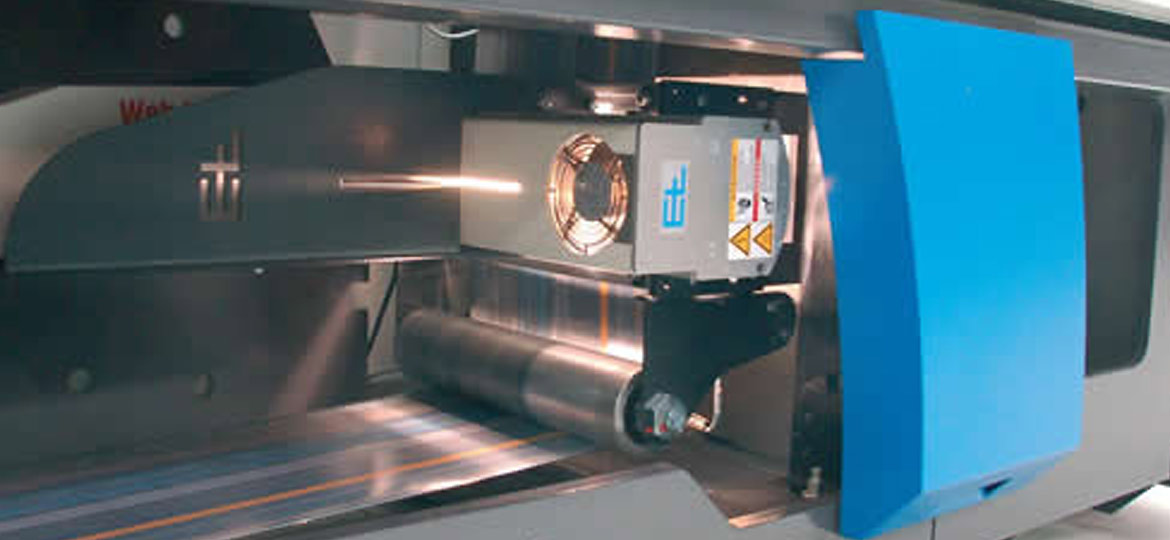
Uma vez que os dados da bobina são concluídos e salvos no servidor central, a equipe do controle de qualidade pode começar a editá-los. A diferenciação é feita entre dois casos, conforme se seguem:
a) Definição de áreas de descartes: elas são automaticamente posicionadas na revisora para retirada do descarte. Isso ocorre predominantemente durante o setup, mas também pode ser durante a produção, devido a ajustes do registro ou problemas com a pressão do cabeçote de impressão, entre outros. Em comparação com o método anterior, essas áreas não precisam mais ser marcadas com pedaços de papel ou post-its.
b) Definição de defeitos individuais: eles são automaticamente posicionados na revisora na mesa de corte. O operador pode, por exemplo, substituir a etiqueta com defeito ou inserir uma emenda. Após a conclusão, o relatório da bobina modificada é salvo no servidor central e fica disponível para o acabamento. Ele é automaticamente transferido do servidor central para o computador da revisora após a etiqueta ser digitalizada pelo de código de barras. Acabamento inicia. O operador simplesmente pressiona o botão “Iniciar” e o sistema para automaticamente, dependendo do tipo de defeito, na mesa de emenda ou na posição do rebobinador de descarte.
Fonte: Revista Inforflexo 130 – Maio-Junho de 2014