Respondendo por 6% do custo das empresas gráficas, os gastos com as tintas representam 1/5 daquele com os substratos. É imperativo que esse custo venha a ser reduzido, sem contar a volatilidade dos preços das matérias primas dependentes do petróleo. Felizmente, os princípios de administração Leanpodem ser aplicados no controle do consumo de tintas e, assim, ajudar a indústria de impressão a transferir para seus resultados esta economia.
Dois grupos de ferramentas auxiliam na contínua identificação e eliminação desses desperdícios. Focando no processo, os 7 desperdícios identificam as causas e consequências da logística deficiente. Além disso, soluções práticas para eliminar desperdícios na sala de preparação de tintas podem ser encontradas no modelo dos 5-S.
- Os 7 desperdícios na Produção
2.1. Superprodução (Overproduction):
Se não há meios de se determinar com precisão a quantidade exata de tinta para um trabalho, muitas vezes, por segurança, produzem-se mais tintas do que o necessário, para evitar faltas e paradas na linha. Preparar, manualmente, a quantidade exata e com a qualidade necessária é extremamente difícil, além de ser um processo demorado, especialmente em uma época de pequenas tiragens e muitas vezes com exigências frequentes do uso de cores especiais, únicas complexas.
Sem um sistema gestor de tintas eficiente, o excesso, invariavelmente, vai para o lixo, já que é praticamente impossível calcular manualmente as sobras que retornam da produção para usá-la em um novo pedido. Como resultado, as empresas que produzem embalagens reportam perder mais de um quarto de seus estoques em excesso de produção de tintas. Na tentativa de evitar paradas de máquinas, algumas delas compram em quantidades maiores tintas pré-misturadas de seus fornecedores – um enorme custo extra.
2.2. Estoque (Inventory):
Os custos de estoque de tinta podem sair do controle facilmente por conta de uma demanda imprevisível, quando ocorre a necessidade de manter uma gama mais diversificada de cores e relativamente de vida curta de prateleira do produto. Os “ativos” estão congelados em excesso de estoques e ocupando o devido espaço para mantê-los.
Dosadores de tintas permitem preparação de todas as cores, a partir de um número limitado de cores básicas, e elimina o inventário de tintas pré-misturadas. Além disso, permite a reutilização e reciclagem de tintas que retornam da produção.
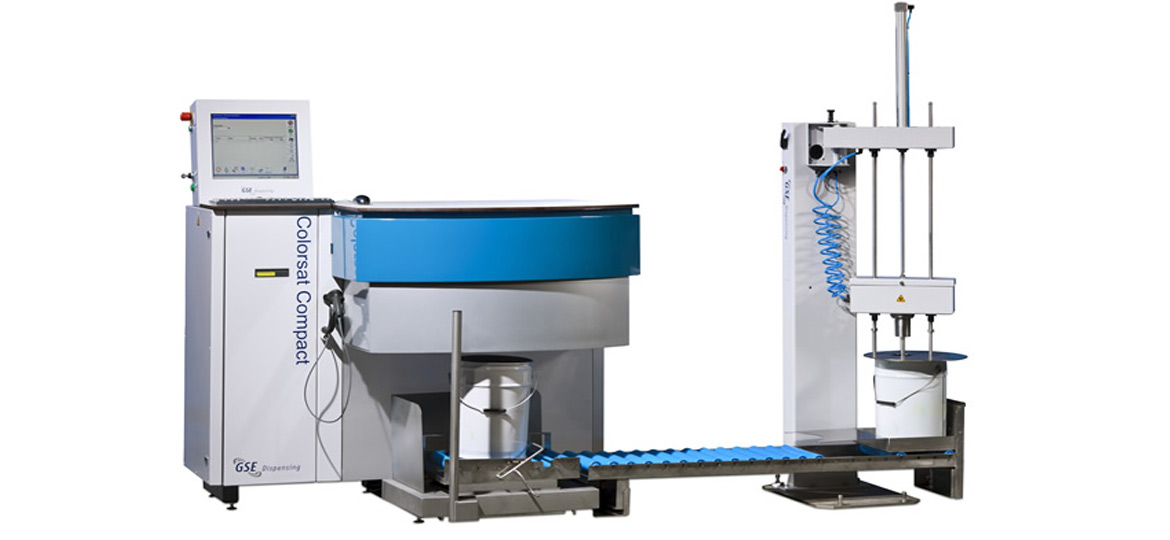
2.3. Movimentação nas operações (Staff movement/ Excess Motion):
Tempo é “matéria-prima”, embora tenhamos uma quantidade finita que podemos utilizar para agregar valor ao nosso negócio. Isso faz do tempo de logística outro fator crítico de eficiência nas empresas. Na sala de impressão, movimento de resíduos resulta em pessoas ou equipamentos em movimento ou caminhando mais do que é necessário para executar o processamento.
Empresas que usam o conceito Lean aperfeiçoam os seus padrões de movimentação para fazer com que estoques de substratos, tintas, equipamentos periféricos e peças de reposição sejam minimizados tanto quanto possível. Isso significa minimizar os despachos, manuseio e transporte de tintas. Um sistema dosador perto da impressora reduz os atrasos logísticos associados à movimentação de tintas pré-fabricadas no estoque.
2.4. Espera (Waiting):
O tempo de máquinas e colaboradores parados é fator chave na caça às ineficiências. Quarenta por cento do tempo de uma produção típica é perdido em setup e ajuste de cor. Ao depender da preparação manual de tintas, o risco de atraso é maior por causa da morosidade do processo envolvido.
2.5. Transporte (Transportation):
Custos com transporte e custos ambientais são reduzidos por meio da aquisição e transporte de tintas básicas em barris de 200 litros, em vez de vários baldes pequenos com tintas pré-misturadas e com maior frequência. Ao preparar com precisão o volume necessário e a qualidade da tinta perto da máquina de impressão, trazem-se resultados, como redução de resíduos e emissões de poluentes, de transporte e descarte de embalagens de tinta.
2.6. Processamento (Unnecessary processing/ Inappropriate processing):
O resultado dos erros na produção ocorre em função do controle ineficiente de matéria prima, ferramental ou design do processo produtivo (chão de fábrica). Produzir as tintas na quantidade exata – com uma precisão de 1g ou menos e na hora certa – significa que qualquer sobra ou retorno da produção pode ser reutilizado na formulação de novas receitas antes do vencimento da validade dessas sobras. Ao misturar a tinta em casa, o empresário obtém maior valor agregado, além da redução de todos os custos das logísticas mencionadas anteriormente.
2.7. Defeitos (Defects):
Tempo gasto para corrigir defeitos também é um desperdício de recursos. Mas isso é inevitável quando não há um sistema de gestão de tintas eficiente em operação. Com um controle que garanta a qualidade dos resultados na primeira vez, o controle do tempo de setup, os processos parados e os rejeitos no substrato são menos prováveis.
A consistência de cores sob controle reduz o risco do erro mais caro de todos: devoluções vindas dos clientes. Um sistema de software de gestão confiável ??torna possível estabelecer processos de rastreabilidade completa das tintas que foram utilizadas e de seus lotes originários, mesmo quando o retorno de máquina for aproveitado na produção de novas receitas.
- A filosofia dos 5-S
Enquanto o modelo dos 7 Desperdícios na Produção nos ajuda a identificar o problema, a filosofia dos 5-S nos mostra uma solução simples para o controle de processos. Auxilia-nos ainda na redução do desperdício, melhoria da qualidade, eficiência e segurança. Os 5 valores de referência dessa filosofiasão estes: Sort (senso de Utilização), Streighten (senso de Organização), Shine (senso de Limpeza), Standardize (senso de Padronização) e Sustain (senso de Disciplina). É um modelo ideal de implementação de gestão enxuta de tinta para a sala de preparação da mesma.
3.1. Seiri (Sort):
O instinto de guardar coisas pode ter sido herdado de nossos ancestrais na savana, uma vantagem de sobrevivência de milhares de anos atrás, mas em um ambiente corporativo, guardar itens, porque eles podem ser úteis algum dia, leva à confusão e desorganização. Seiri, a utilização, nos ensina a ser mais exigentes e quebrar o hábito de guardar coisas. Requer que se mantenham os itens mais utilizados na sala de preparação de tintas em locais de fácil acesso – colocar os menos utilizados em áreas distantes e descartar aqueles desnecessários. A ideia é a de garantir que tudo deixado na sala de tinta esteja relacionado com a preparação das tintas. Manter a sala de tintas arrumada, melhora a busca e a eficiência em encontrar o que é necessário, além de deixar limpo o espaço.
3.2. Seiton (Straighten):
Esta etapa está relacionada ao correto armazenamento de itens como baldes limpos, papel para impressão de etiquetas, tintas retornadas da produção em seu lugar designado para que possam ser acessados facilmente e rapidamente. O lugar de cada item deve ser claramente identificado, e cada item deve ser organizado de uma forma que promova o fluxo de trabalho eficiente. Além disso, os itens usados ?com maior frequência devem ser os de mais fácil acesso, sem que o operador tenha que se abaixar para alcançá-los.
3.3. Seiso (Shine):
Após a primeira limpeza completa posterior à implementação do 5S, limpezas diárias de “follow- up” são necessárias a fim de manter essa melhoria. É uma maneira eficaz de identificação de inconsistências, e da mesma forma, ajuda a construir a primeira impressão vital de profissionalismo quando da visita de um potencial cliente. Limpeza das válvulas dosadoras de tintas após cada turno, e toda a sala de tinta uma vez por semana, deve ser rotina. Os pingos e derramamentos no piso devem ser limpos imediatamente.
3.4. Seiketsu (Standardize):
Velhos e maus hábitos são difíceis de serem eliminados. É por isso que o terceiro ‘S’ abrange classificação, padronização, limpeza, etc. que devem se padronizados para evitar que os colaboradores não percam o “momentum”, escorregando de volta para a velha atitude. A aderência é maximizada se todos souberem de suas responsabilidades e as ações relacionadas ao 3º S podem ser detalhadas na descrição de cargos de seus colaboradores, por exemplo.
3.5. Shitsuke (Sustain):
Uma vez que a nova forma de operar se torna padronizada, ela é enraizada na cultura corporativa, através de revisões regulares, bem como a abertura a novas ideias e melhorias no processo de trabalho. Como as empresas são entidades dinâmicas, os padrões internos devem evoluir, adaptando-se às novas circunstâncias. Shitsuke indica que a melhoria é um processo contínuo sem fim!
- A tecnologia de preparar tintas, automaticamente
Um processo logístico, organizadamente simples, é essencial para responder a esses desafios. Esse método rápido, preciso e abrangente de entrega de tinta para o processo de impressão, também conhecido como “cores sob demanda”, melhora a qualidade, reduz os níveis de estoque e aperfeiçoa o controle de inventário, permitindo melhores margens e um produto ainda de maior qualidade.
O software de integração de informações e padrão de gestão, por exemplo, fornece informações em tempo real sobre a disponibilidade de uma receita e a combinação de cores instantaneamente, sobre o ajuste instantâneo de cores, a análise de custo detalhado de cada ordem de produção e a capacidade de rastrear tintas utilizadas em cada receita para o número do lote base original.
A tecnologia básica de um fluxo de trabalho automatizado de logística de tintas compreende um sistema dosador gravimétrico, com uma interface amigável, ligada a vários barris de tintas básicas (variando de 8 a 20). Válvulas resistentes à corrosão de aço inoxidável com características dinâmicas de fluidos otimizados completam o processo, garantindo a rápida e precisa preparação.
Vale lembrar que o preço é apenas um dos custos agregados às tintas e sua importância é relativa aos inúmeros custos ocultos (como transportes, impostos, resíduos, armazenagem, devoluções e gastos administrativos, apenas para citar alguns), normalmente os mais altos e perigosamente enganosos. Uma boa gestão de tintas, do controle das cores básicas até o produto acabado, é a chave para manter os custos sob controle.
Em suma, um sistema de distribuição de tintas gravimétrico, com a especificação correta, com confiabilidade e suporte, vai garantir a qualidade de impressão e fidelidade, o controle de orçamentos e, ainda, vai apoiar o crescente nível de gestão Lean, uma vez que os processos industriais se tornam aliados de automatizações, contrariamente aos manuais.