OS DOIS PROCESSOS NÃO EVOLUÍRAM NA MESMA VELOCIDADE NAS ÚLTIMAS DÉCADAS, NO ENTANTO, SEM QUALIDADE, O CORTE E VINCO INVIABILIZARÃO TODO O LOTE DE UMA EMBALAGEM DEPOIS DE IMPRESSA
1 – Introdução
Atuo no setor de corte e vinco rotativo de papelão ondulado desde os anos 80. De lá para cá, o processo de impressão evoluiu muito, porém, o de corte e vinco continua praticamente o mesmo daquela época. Parece ter sido esquecido tanto na sua importância de valor como nas melhorias do processo. Em vez de uma evolução, tivemos um retrocesso.
Impressão versus corte vinco: a impressão em si possui suas variáveis, mas conta com equipamentos modernos, que minimizam e até evitam os possíveis erros, diminuindo a parte manual, entre outras melhorias. Já no corte as variáveis são muitas também, pois os insumos são inúmeros e ainda há a montagem das “formas”, ou clichês metálicos, que é manual.
Neste artigo, orientaremos sobre como se monta uma forma com qualidade e padrão, mas antes apresentaremos os insumos e demais produtos envolvidos nessa etapa tão importante do processo de corte e vinco, pois cor, dureza, fornecedor, nada disso indica a qualidade de um bom produto.
Vale destacar, primeiramente, que o “achismo”, o famoso “jeitinho” e “gambiarra” não podem mais existir. E que a união em toda a cadeia do papelão, a comunicação e informação sobre todos os produtos envolvidos na montagem da forma são fundamentais para a qualidade final do corte e vinco da embalagem de papelão ondulado (PO).
Exemplos da falta de comunicação são inúmeros, só para citar alguns: o perfil da onda de PO foi modificado tempos atrás e isso passou a requerer um pouco mais de cola – os fabricantes de insumos não foram informados; o uso externo ou interno de impermeabilizantes na composição do papel ou aplicado sobre a superfície do PO impacta diretamente no corte, já que no papel as fibras são pequenas devido à reciclagem. Pergunto: alguém informou aos fabricantes das lâminas de corte sobre tais modificações, para ajustarem os seus produtos? Não.
Temos a cultura de achar que tudo o que vem de fora é melhor do que o nosso. Bom exemplo é dos carros importados que fazem14 a17km/Lt nos EUA e Europa, mas no Brasil consomem10 a12km/Lt, porque a gasolina de fora tem alta octanagem, enquanto a brasileira é misturada com álcool e nossos motores têm regulagem também para álcool, daí a baixa quilometragem, entre outros itens diferentes. No caso da embalagem de PO ocorre a mesma situação: qualidade, umidade, tempo de cura, fibras diversas, projetos de embalagens, entre outros, são diferentes daqueles utilizados lá fora. Então, temos também que “nacionalizar” nossas formas. Estão surgindo modelos de alta “performance”, padrões europeu e americano. Precisamos ter o nosso padrão, não simplesmente corrigir trocas, lâminas de aço, borracha. Por tudo isso, trabalhar em conjunto (em toda a cadeia do papelão) e buscar os valores básicos que foram deixados para trás são os novos caminhos daqui para frente.
2 – Produtos e serviços envolvidos no processo de corte e vinco
2.1. Os produtos que entram no corte são estes: calhas de madeira, borrachas, elastômero, aço, cola, mantas de poliuretano. Cada um deles possui suas “especificações técnicas” e testes para a aprovação de sua qualidade.
2.2. Os serviços, se assim podemos chamá-los, são: os faqueiros com sua mão de obra e também o setor de desenvolvimento de projetos de layout das embalagens. Se esses dois não trabalharem em conjunto, teremos perdas e baixo rendimento de produção.
2.3. Os faqueiros são profissionais ou empresas que, com sua mão de obra praticamente artesanal e conhecimento, fazem as formas ou clichês metálicos. Hoje temos equipamentos que podem auxiliar nesta parte artesanal, como o dobramento das lâminas de aço, e também nos cortes das calhas de madeiras, mas sempre temos a parte artesanal, sem ela não há resultados.
2.4. O setor de desenvolvimento de embalagens (o que projeta o layout das mesmas) precisa ter conhecimento sobre cada produto (insumos) e também sobre como é feita a confecção das formas, ou clichês metálicos; sem esse conhecimento, o projeto pode nascer com problemas e dificultar a produtividade e a qualidade.
Então esses dois setores, os faqueiros e o desenvolvimento, têm que trabalhar em conjunto para que tenhamos um projeto eficaz.
3 – Qualidades básicas dos produtos para se fazer uma forma, ou clichê metálico
3.1. Calhas de madeira. A espessura é de12 a13 mm, seu comprimento é conforme o do cilindro da impressora, ou da embalagem a ser feita. Diâmetro interno: este é de acordo com o diâmetro do cilindro da impressora, com uma tolerância de 5.0mm menor. Comprimento do diâmetro nunca deve passar da metade do diâmetro da forma. Superfícies, interna e externa, devem ser feitas com madeira adequada para que não haja lascamentos e sejam isentas de cerdas, isto é, lisa e sem ondulações.
3.2. Borrachas: feitas sempre com um composto que forme células fechadas para se obter um melhor efeito mola. Dureza: existem várias durezas conforme a sua aplicação na forma e estas não podem variar mais que 3 pontos em Shore A. Superfícies: sempre porosas para facilitar a colagem. Espessura: também há várias espessuras conforme a aplicação na forma, podendo variar no máximo1.0 mmpara mais.
3.3. Poliuretano expandido ou elastômero: mais conhecido como ”celastro” (a marca do produto), mais utilizado no interno de vazadores ou sloters e segue os mesmos padrões das borrachas.
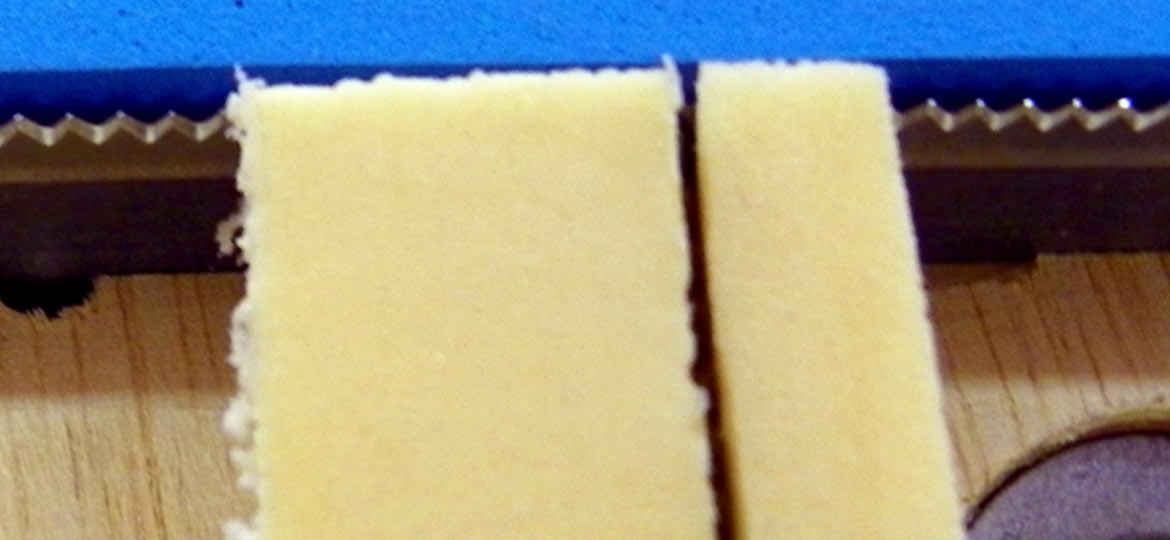
3.4. Aço: designação de aço com médio teor de carbono e dureza de 37 a40 HRC, com uma estrutura cristalográfica bainítica, pois esta estrutura é que vai dar a ductibilidade – flexibilidade para fazer as dobras sem trincas ou microtrincas. Espessura: de 1.40 a1.42mm. Característica física isenta de: abaulamento na largura; empeno lateral; coil set ou curvamento; hélice ou torção; bordas tratadas. Teste de dobras para sua aprovação: 40, 90, 180 graus, seguindo padrões internacionais. A matéria prima é a mesma para confecção de vincos, picotes e cortes. Para cada produto final existe uma especificação técnica, seguindo padrões internacionais e nacionais.
3.5. Cola: designada para fazer a colagem das borrachas e o elastômero “celastro” nas formas de madeira. Deve ser de secagem rápida e aplicada nas borrachas e em pequena quantidade, ou o máxi possível, pois se usada em excesso, vai causar a perda do efeito mola em até 30% e também provocar histerese, isto é, deterioração da borracha na metade da sua espessura, devido ao aumento do calor gerado pelas batidas.

4 – Mantas de poliuretano
4.1. Mantas de poliuretano. Na lista de problemas existentes atualmente no setor de corte, a manta de poliuretano está presente em todos. Sua dureza está ligada ao perfil de corte utilizado; no Brasil este perfil é o prisma e a dureza necessária é de 86 a 88 Shore A com a média de 87 – padrão internacional. A espessura é conforme a determinação do fabricante da impressora, com uma tolerância máxima de 1,0mm para mais. A superfície tem que ser retificada, isto é, não podendo ser lisa brilhante com aparência de lixada, para que esteja uniforme em toda a sua extensão e que o conjunto tenha o mesmo padrão, sem altos e baixos, para que também absorva a tinta da impressão e não repasse para a próxima caixa. O reforço interno pode ser de aço ou tala de fibra, o melhor é o de aço, mas tem que ser um aço com baixa deformação. O de tala de fibra precisa ser tratado, não pode ser quebradiço para evitar expansão no comprimento e no diâmetro, evitar deformação gerando bolhas na sua superfície. A largura segue especificação do fabricante da impressora, com tolerância 0.50mm para mais e para menos, sempre com as bordas em 90 graus.
5 – Como montar uma forma de qualidade e com padrão
5.1. Corte das calhas de madeira. Hoje no Brasil temos dois tipos: manual com serra tico-tico e com serra cutoal e o corte a laser. Corte manual é ainda o melhor no sentido de fixação dos aços, pois seu perfil de corte forma pequenas ondulações na sua extensão. A largura deste corte é de 1.20mm com uma variação de 0.05mm para mais ou para menos. Este corte depende da habilidade do serrador em manter o traçado, para que não haja variação no dimensional. Corte a laser: tem uma precisão no dimensional, pois é feito no computador ”CNC”. A largura sua largura é de 1.10mm, pois o corte a laser não é paralelo, tanto que os americanos o chamam de “perfil ampulheta”. A formação de carbono pela madeira pode provocar deslizamento das lâminas, por isso este corte requer cuidados para evitar esses problemas. Cada tipo de corte requer calhas de madeiras específicas para que se tenha um bom resultado.
5.2. O projeto da forma tem que ser em comum acordo entre o usuário “departamento de desenvolvimento” e o faqueiro, que vão definir altura de corte, número de dentes, altura do vinco, junção de lâminas, diâmetro dos vazadores, largura de sloters, largura dos refiles laterais para se obter os insumos adequados, tanto aço como borrachas.
5.3. As junções, ou encontro das lâminas, têm que ser perfeitas, não passando raio de luz.
5.4. O corta refiles, tanto os laterais quanto os das lâminas de entrada e saída, precisam ter uma junção perfeita, tanto no corpo quanto no corte utilizando o perfil chamado de “biquinho”, isto é, ele acompanha a inclinação do perfil de corte das lâminas.
5.5. As borrachas e elastômeros têm de estar na quantidade certa nos lugares certos. O excesso de emborrachamento pode provocar variação dimensional da caixa.
Os furos de fixação da forma no cilindro: o diâmetro do furo não pode ser mais que 30% do diâmetro do parafuso original da impressora e com arruela. Rebaixo do furo: este rebaixo é feito para se encaixar a arruela e também para não expor muito a cabeça do parafuso sobre a forma, ele não pode exceder a 40% da espessura da madeira, isto é 5.0mm. Distância entre os furos deve ser no máximo, tanto no sentido de rotação quanto na horizontal 150×150 ou 200×200. A maior quantidade de parafusos tem que estar aonde tiver maior concentração de aço.
6 – Fixação da forma no cilindro da impressora
6.1. A superfície do cilindro deve ser lisa, sem ranhuras profundas, sem bordas de parafusos quebrados.
6.2. Em toda furação para os parafusos as roscas devem estar em bom estado, ou com os incertos com roscas boas, não pode haver furos inutilizados. A borda dos incertos deve estar paralela ou abaixo da superfície do cilindro.
6.3. No cilindro tem que haver a marcação zero, isto é, um rebaixo em linha feito no cilindro para alinhar a borda da forma, ou uma régua para encostar a forma e deixá-la nivelada ao cilindro.
6.4. Sistema de aperto: deve ser manual com chaves fixas de boca ou catraca e com parafusadeira pneumática. Em qualquer sistema, sempre colocar as primeiras voltas do parafuso com a mão para verificar se os furos da madeira estão alinhados ao cilindro, então se faz o aperto seguindo regras do próximo item. Nunca colocar os parafusos diretamente com a parafusadeira, pois, corre-se o risco de se estragar as roscas. Se a furação madeira x cilindro não estiverem certas, avise o supervisor.
6.5. Regras para fazer o aperto: pode ser do centro da forma para as extremidades em formato de estrelas, ou do centro para as extremidades, em linha. O princípio é este: existem dois corpos e estes têm que virar um só, sem apresentar bolhas entre a madeira e o cilindro.
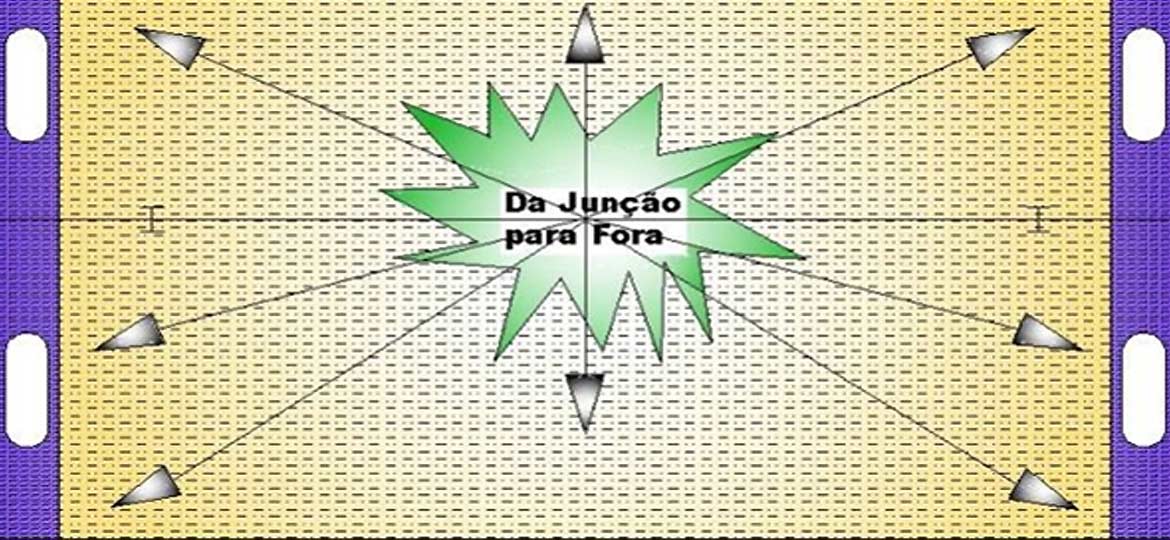
7 – Conclusão
Todos os itens citados anteriormente são básicos, há muito ainda a dizer sobre cada um deles, para não incorrermos nesta lista de problemas: vinco falso, refile aderido, fora de dimensional, desgaste prematuro das mantas, quebra de lâminas, lâminas soltas, entre outros.